
Featured Guide
Ultimate Guide to Leadership Development
DDI’s Ultimate Guide to Leadership Development gives HR pros everything they need to create and launch powerful leadership development experiences.
ReadResource Type: All
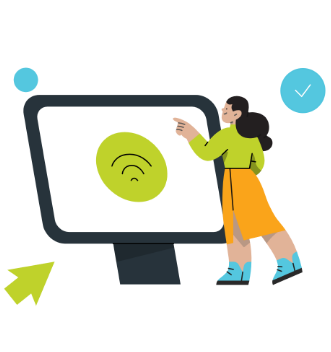
SUBSCRIBE
Leadership news straight to your inbox
Subscribe to curate your preferred list of leadership research, blogs, podcasts, newsletters, webinars, and more that comes to your email inbox hot off the press.